- topics
- Why Jigsaw Puzzles?
- Inspiration for the Shape of the Pieces
- How we generate the pieces
- Whimsy Guide
- About the Artwork of Jonathan Mccabe
- Process - the making of
- What's Next?
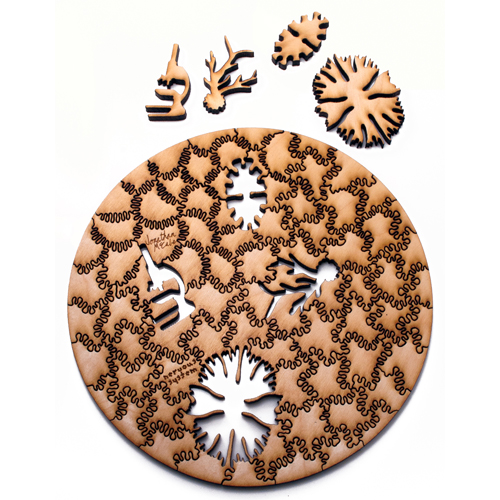
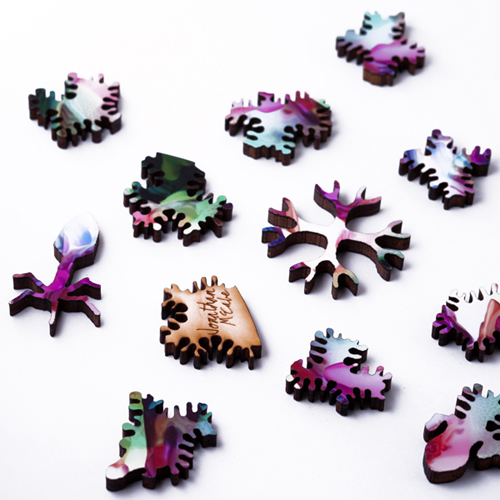
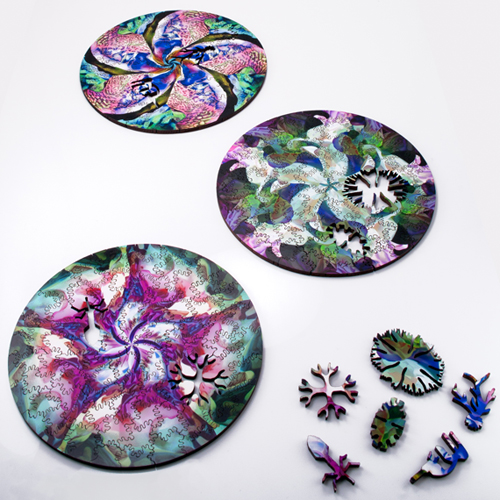
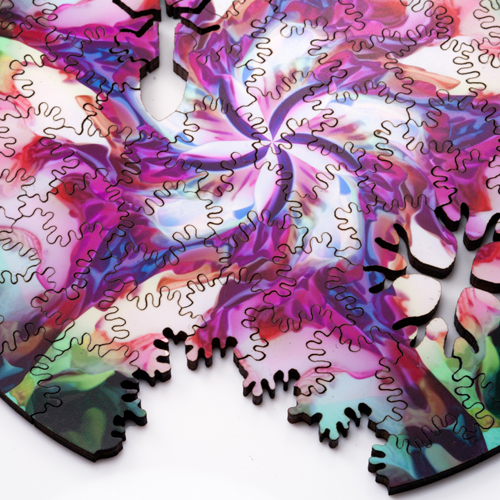
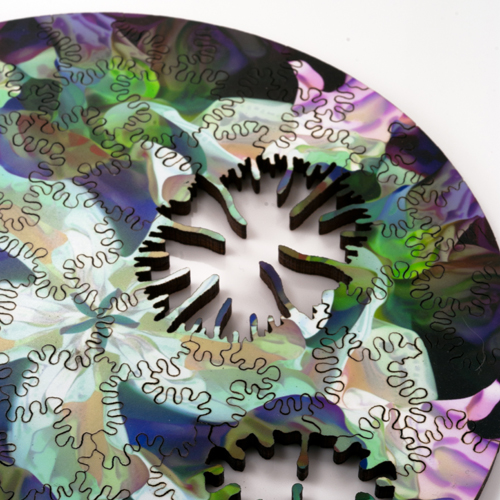
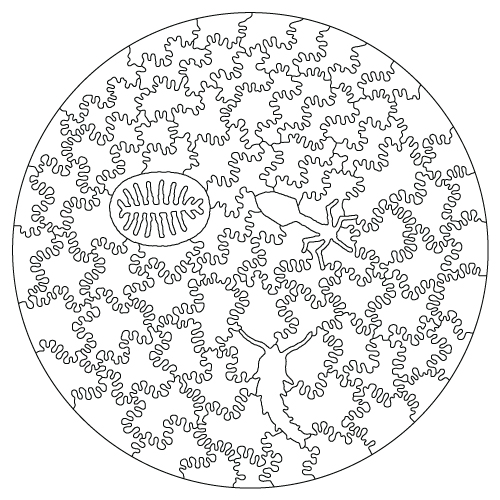
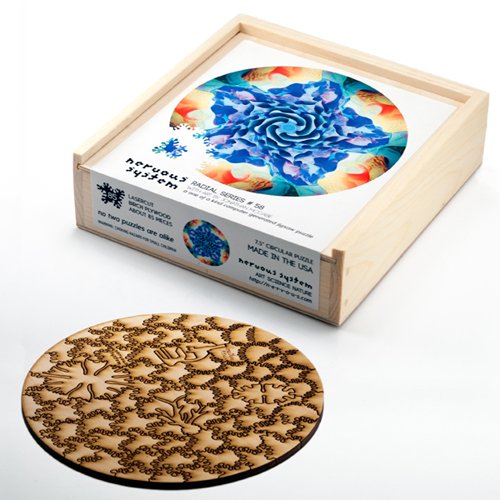
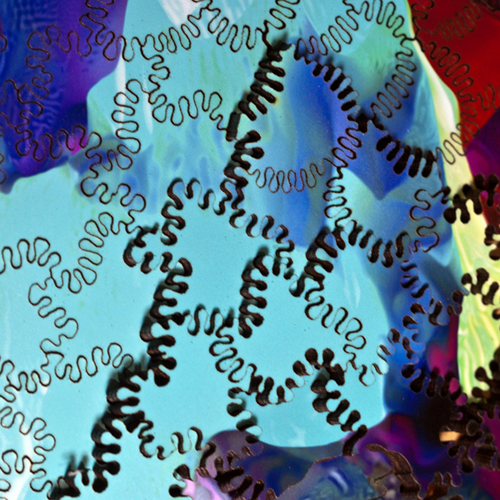
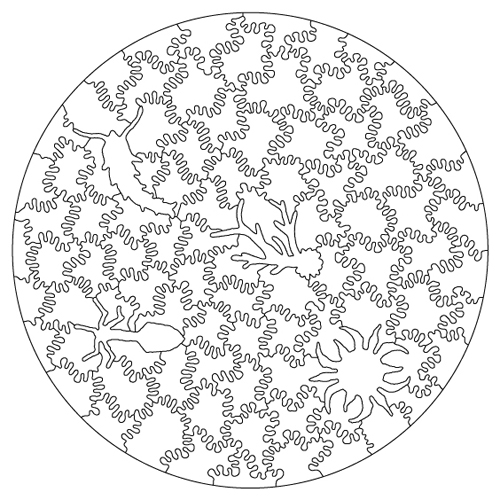
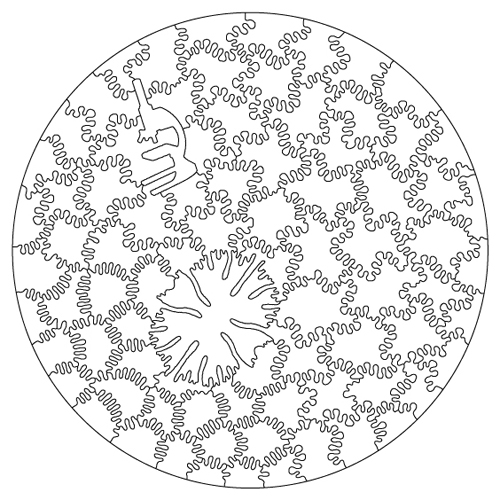
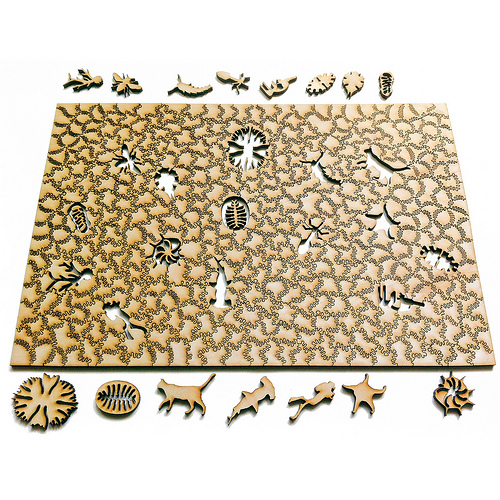
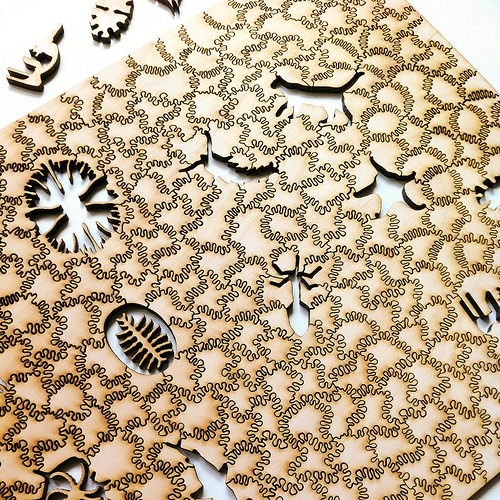
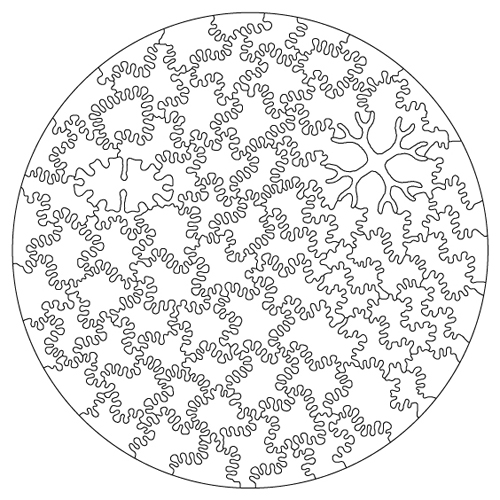
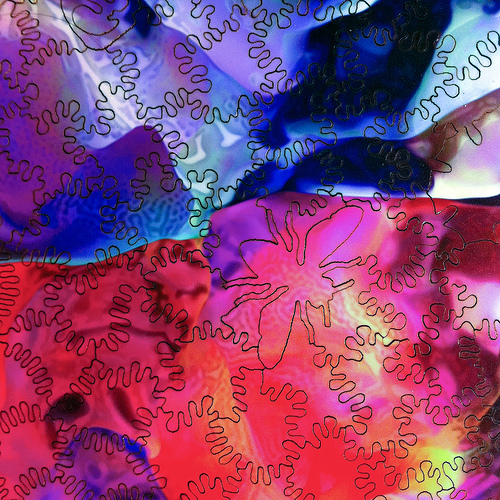
the first 50 Radial Puzzles and the first 12 McCabism Puzzles are available now in the Nervous System shop
The first was a trip to Paris. A tip from a travel guide sent us to Puzzle Michèle Wilson, a small shop specializing in traditional wooden jigsaw puzzles. As you enter, an artisan sits to your left cutting a tidy stack of plywood sheets with a scroll saw. She isn't following a prescribed pattern and hence each time she cuts, she creates a different puzzle. The results are dissimiliar from the gridded bits of cardboard we knew in childhood. The pieces were all unique shapes, incorporating funny curves, spirals and even surprise pieces shaped like recognizable figures. Freed from the constraints of mass production, puzzles were suddenly more exciting and creative.
It turns out that jigsaw puzzles have a long history. Wikipedia tells me that a London map engraver named John Spilbury first commercialized them in 1760. He painted images on wood and then cut them into tesselating pieces with a jigsaw. It wasn't until the 1930's that hydraulic presses began to be used to create jigsaw puzzles from cardboard. While these cardboard puzzles could be sold at a low price, the great expense of creating the cutting die meant that the same cutting pattern would be used for every puzzle and the shapes of pieces had to be limited to shapes easy to produce a die for. Recently computer controlled cutting tools like the laser cutter and waterjet have opened up new avenues for jigsaw puzzle production. We can produce a high quality, archival puzzle in wood with the uniqueness and artistry of a handcut puzzle for prices more competitive with mass produced cardboard stuff. Companies like Liberty Puzzle in Colorado and Wentworth Puzzle in the UK have been applying lasers to jigsaw puzzle craft for a few years now, yet the results are rather traditional. Should the laser cut puzzles of today, look the same as the handcut puzzles of the 18th century? And why use a laser to cut hundreds of identical puzzles? We wanted to make puzzles for the 21st century.
This is a 110 million year old fossil Cleoniceras Ammonite found in Madagascar. Ammonites are extinct cephalopods that lived in shells and roamed the ancient oceans. Their closest living relatives are the Nautiluses, Octopi, Squid, and Cuttlefish of today. Like the Nautilus, Ammonites gradually add onto their shell to accommodate their increasing body mass. As they extend their shell they build a wall that closes up the now too narrow portion of the shell behind them.
photos of a Nautilus. cut in half (left) by Jitze1942. alive (right) by PacificKlaus
Now the really cool thing about the Cleoniceras Ammonite, is that unlike the Nautilus, the morphology of the tissue wall it built between its chambers was not just a smooth curved wall. Instead it was a bizarrely complex fractal 3-dimensional shape. These patterns are called “suture patterns” and they mark the intersection of the septum walls with the shell. Scientists can’t agree why the septum walls are so complexly furrowed or even how they formed. But, they certainly have published many conflicting arguments about the subject.
a snapshot of the theories
Ø. Hammer proposes a reaction-diffusion explanation for the formation of suture patterns (on the far right)
A. Checa and friends propose a viscous fingering explanation, where the two fluids at play are the cameral liquid and connective tissue (on the right)
F.V. De Blasio uses finite element analysis to argue that the high sinuosity is an evolutionary response to external pressure, reinforcing the shell in response to hydrostatic pressure
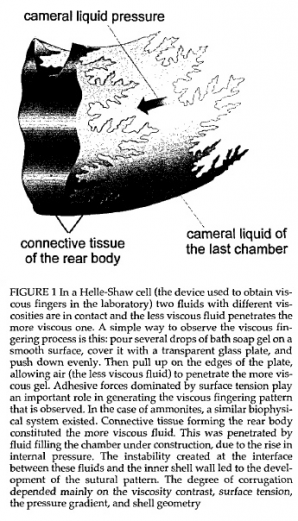
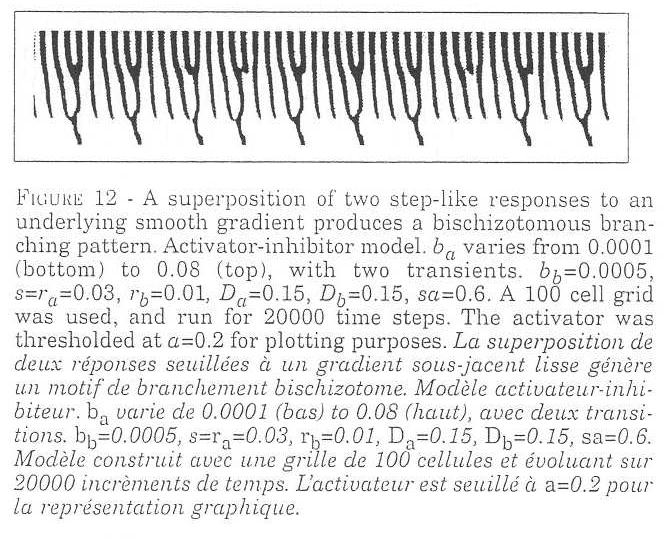
- Here's some references if your are interested in the topic:
- Hammer, Ø. 1999. The development of ammonite septa: an epithelial invagination process controlled by morphogens? Historical Biology 13:153-171.
- Hammer, Ø. & Bucher, H. 1999. Reaction-diffusion processes: Application to the morphogenesis of ammonoid ornamentation. GeoBios 32:841-852.
- García-Ruiza, J. & Checa, A. 1993. A model for the morphogenesis of ammonoid septal sutures. GeoBios 26:157-162.
- Lewy, Z. 2002a. The function of the ammonite fluted septal margins. Journal of Paleontology, 76::63-69
- De Blasio, F.V. 2008: The role of suture complexity in diminishing strain and stress in ammonoid phragmocones. Lethaia 41:15–24.
We thought these interlocking suture pattern would make amazing puzzle pieces, but as no one can agree on how they form, we were left on our own to explore the possibilities. Our first instinct led us to investigate the proposal of A. Checa, and look into pattern formation through viscous fingering. This is a fluidic phenomena where two fluids of differing viscosities are forced into one another, forming blob-like, branching shapes. We were led off into a tangent experimenting with Hele-Shaw cells, a physical experiment for forming viscous fingering patterns.
We also researched techniques for simulating Hele-shaw cells. Unfortunately, these proved too computationally intensive for the complex patterns we need for generating puzzles. The figure below shows a Hele-shaw simulation that took 50 days to compute.
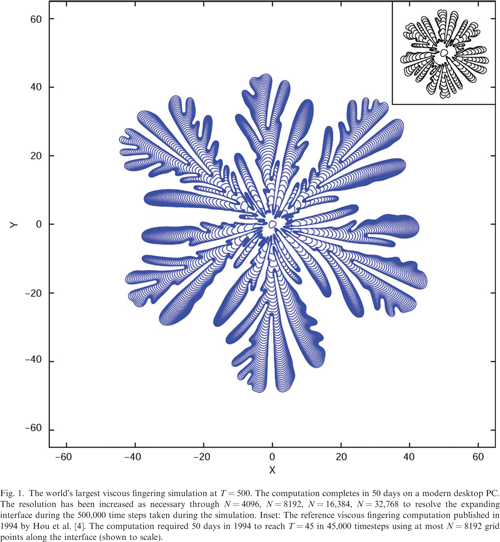
However, it turns out that viscous fingering is a subset of a broad category of natural and mathematical phenomena called Laplacian growth, which includes lightning, coral growth, crystal growth, the structure of random matrices, and more. In fact, one of our original jewelry lines, Dendrite, is based on a type of Laplacian growth called Diffusion Limited Aggregation! All of these processes share a common branching morphology as well as a similar underlying mathematical structure. Eventually, we started experimenting with using simulations based on a type of Laplacian growth called dendritic solidification which led us to create a branching puzzle cut.
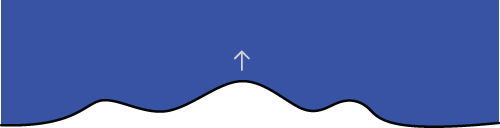
Our simulation uses a phase-field technique based on research by Ryo Kobayashi. Phase-field models avoid explicitly representing boundaries by replacing a discontinuous phase transition with a smooth transition in an order parameter $p \in [0, 1]$ over a boundary of thickness $\epsilon$ from 0 (solid) to 1 (liquid). So rather than defining geometric regions of solid and liquid, there is a phase parameter defined everywhere in space.
Applying the phase field approach naively to the problem of generating jigsaw puzzles introduces a few problems. Dendritic solidification typically involves a single material in one phase encroaching on another phase of the same material, e.g. a single, solid piece of ice growing into an expanse of supercooled water. In this setup, one phase grows while another shrinks. We would prefer the simulation to be piece-agnostic and symmetric with respect neighbors’ phases. Rather than one piece acting in a ”growing” role and another in a ”shrinking” role, the boundary should evolve symmetrically, with identical dynamics in both directions. Otherwise, we introduce an aesthetic asymmetry in the quality of adjacent pieces’ boundaries.
To address this issue, we have to ignore our intuitive notion of the “phases of matter”. The equations governing the dynamics are symmetric, so instead of a solid crystal growing in a supercooled liquid we can think of a liquid growing into a “superheated” solid. Indeed, we can have the liquid state be supercooled and the solid state be superheated simultaneously in simulation space. This allows both phases to grow into one another symmetrically.
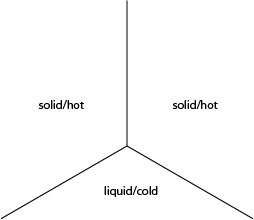
However, we have a further complication when multiple pieces meet. We cannot define each piece as “solid” or “liquid” without confusing the pieces together. Instead each piece needs to be defined as its own phase. Here we are completely abandoning our previous idea of phase and simply labeling each piece with its own parameter that represents an abstract phase. Additional each "phase" requires an independant "temperature". This technique is typically used in a grain boundary simulation, where the phase might represent something completely different such as crystal orientation. So we have developed a notion of a multiphase model of dendritic solidification.
This process could be done in any number of ways. We choose to define pieces by a kind of generalized voronoi diagram. Rather than computing the voronoi diagram directly, we define a number of seed shapes in simulation space, and allow those shapes to diffuse out until they meet neighboring shapes. This is a kind of reaction-diffusion, which allows us to easily define arbitrarily complex boundaries and seeds. Defining seeds with different shapes and spatial density allows us to make different styles of puzzle piece
Before the simulation begins, the piece boundaries are given an initial oscillating perturbation of simple sin waves. Experiments and simulations show that dendritic solidification is very sensitive to the initial seed shape that it grows from. Different wavelengths and amplitudes yield differing morphologies of growth. Therefore, this initial perturbation is one of the main parameters we vary to change the cut style
This procedure removes all small blobs and many thin regions. However, some thin regions may still exist. To reduce these, first we convert our pieces, which are defined by a spatial grid of phase parameters, to geometric boundaries. This is done through a modified marching squares algorithm. We then detect any points that are too close to another line. These points then undergo Laplacian smoothing, which tends to reduce the folds that cause thin regions. This process is repeated until no points are detected too close a boundary. The lines are then export for cutting.
For even more technical detail, you can see this draft of a paper we wrote: Multiphase Numerical Modeling of Dendritic Solidification for Jigsaw Puzzle Generation
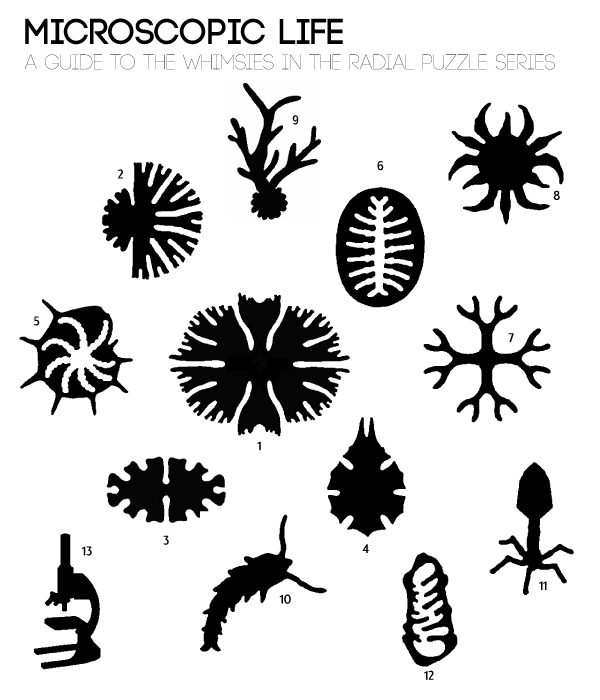
- Algae Micrasterias apiculata, single cell from above
- Algae Micrasterias thomasiana, half during cell division
- Algae Euastrum pecten, single cell from above 1,2 & 3 - freshwater green algae from the Desmids orders. Though unicellular they are divided into two compartments separated by a narrow bridge. Each compartment contains one chloroplast and no flagella.
- Algae Pediastrum darwinii
another type of nonmotile green algae that inhabits freshwater environments. They are coenobial which means they form a colony containing a fixed number of cells, with little or no specialization - Foram Lenticulina anaglypta
this Foraminifera is a marine amoeboid protozoa that forms its shell from calcium carbonate - Diatom Campyloneis grevillei top view
diatoms are unicellular algae encased within a cell wall made of silica. - Radiolarian Tetracranastrum bifurcatum
- Radiolarian Collosphaeridae sp.?, single animal 7 & 8 - Radiolaria are unicellular eukaryotes that produce intricate mineral skeletons of silica
- Amoeba Amoeba Proteus in active stage
This small protozoan uses tentacular protuberances called pseudopodia to move and phagocytose smaller unicellular organisms. From Leidy “a ramose individual with the posterior part as a mulberry-like mass” - Copepod Clytemnestra scutellata female
a small planktonic marine crustaceon - myovirus bacteriophage
a virus that infects bacteria, it carries genetic material such as DNA in the outer icosahedral protein capsid which it injects into a host cell - Mitochondrion
a membrane-enclosed organelle found in most eukaryotic cells. theyare sometimes described as "cellular power plants" because they generate most of the cell's supply of adenosine triphosphate (ATP), used as a source of chemical energy - Optical Microscope
a type of microscope which uses visible light and a system of lenses to magnify images of small samples. Optical microscopes are the oldest design of microscope and were possibly designed in their present compound form in the 17th century
1,3,4,5,6,7,8,10 are based on drawings from ‘Kunstformen der Natur’ by Ernst Haeckel, 1899
9 is based on a drawing from 'Fresh-Water Rhizopods of North America' by Joseph Leidy, 1879
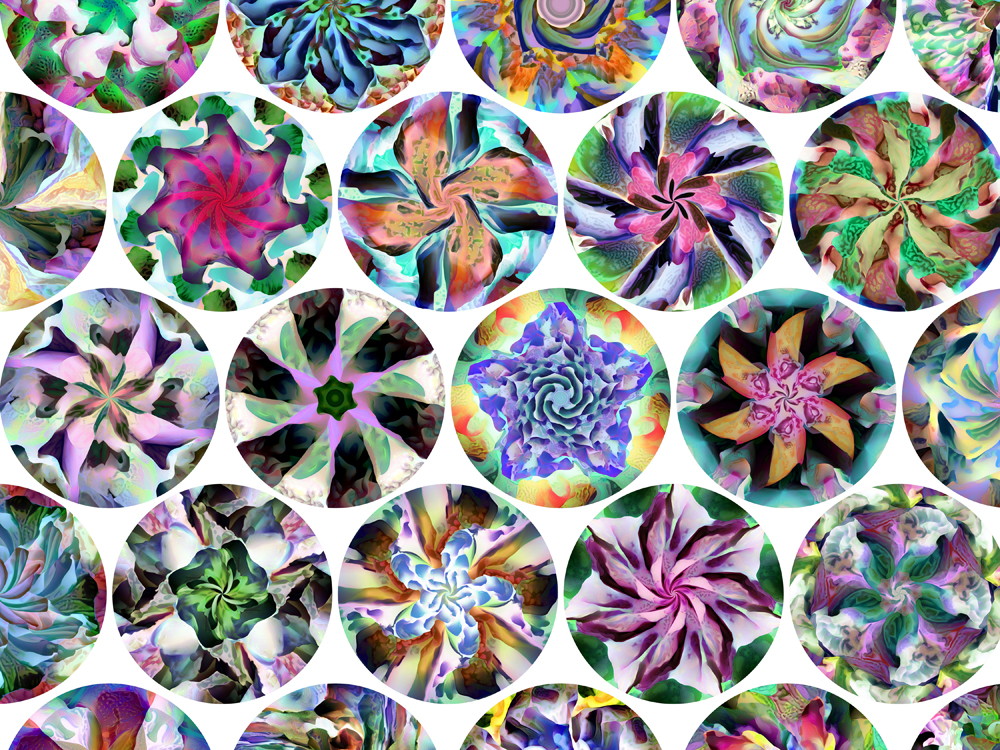
We are huge fans of Jonathan McCabe, a generative artist whose work we first came across on Flickr. We thought the colorful landscapes of his reaction-diffusion works would be perfect for jigsaw puzzles and luckily, he thought so too! Here is how he describes his designs for the radial puzzle series.
We showed our first test puzzle at the Eyeo Festival in June 2011. It looked like this:
At that point the piece shapes were still underdeveloped but the system was working overall (ie. we were able to grow interlocking pieces). But it took us a lot of experimentation with our system and exploration of our parameter space before we arrived at a good cut style.
this video was our first attempt to browse the parameter space
here's one of our piece shape studies from later in the project
And some sketches about how to change the shape of our grid or create multiple grids in each puzzle and how to incorporate whimsy figures
Ultimately, we arrived at some promising results, a family of interrelated cut styles that can be varied through space.
But then we encountered a new problem. How do we turn these images into actual physical puzzles?
- Wood - The first thing we did was buy a laser cutter. A 60W Epilog was the best we could afford and it seemed powerful enough to cut through 1/4" plywood. But not all plywoods are great for laser cutting. Many contain very reflective glue layers that make them difficult to cut by laser. Others have voids and strange filler materials inside that cause the laser to cut unevenly. This means you could end up with a
puzzle that is cut out everywhere, except in a few spots. This is a big problem, because you can't tell that some spots aren't cut until you remove the wood from the machine and flip it over; at that point it's too late to fix it. The image below shows an early test cut on a 1/4" italian poplar plywood where one spot didn't cut through due to inconsistensies and filler in the wood. Ultimately, we fixed this problem by finding the right plywood, a good two sides 3-ply birch which cuts quite consistently.
- Image - Every single puzzle has a different picture. This means we can't just go to a printer and ask them to print 100 copies of an image. We needed to find a printer would would affordably print one offs for us. It turns out such a printer didn't exist. So we bought our own pigment inkjet printer that can print images up to 13x19". Then we tested a wide range of "archival" photography papers for both their printing and laser cutting properties. Each image is printed in our studio, then mounted on the plywood with archival spray mount.
- Paper burns - the number one problem with laser cutting a printed image is the tendency of that image to get crispy and discolored. So we had to come up with a combination of protective sprays and physical masking that worked for our puzzles. This took us a while.
- Packaging - The puzzles needed retail ready packaging for stores which again presents the issue that every puzzle has a different image. We make one standard cardboard box for all our puzzles. So we worked with a box maker in Vermont to create slide top wooden boxes and a local printer to create adhesive labels, each with a different puzzle image on them.