Xylem Arbor
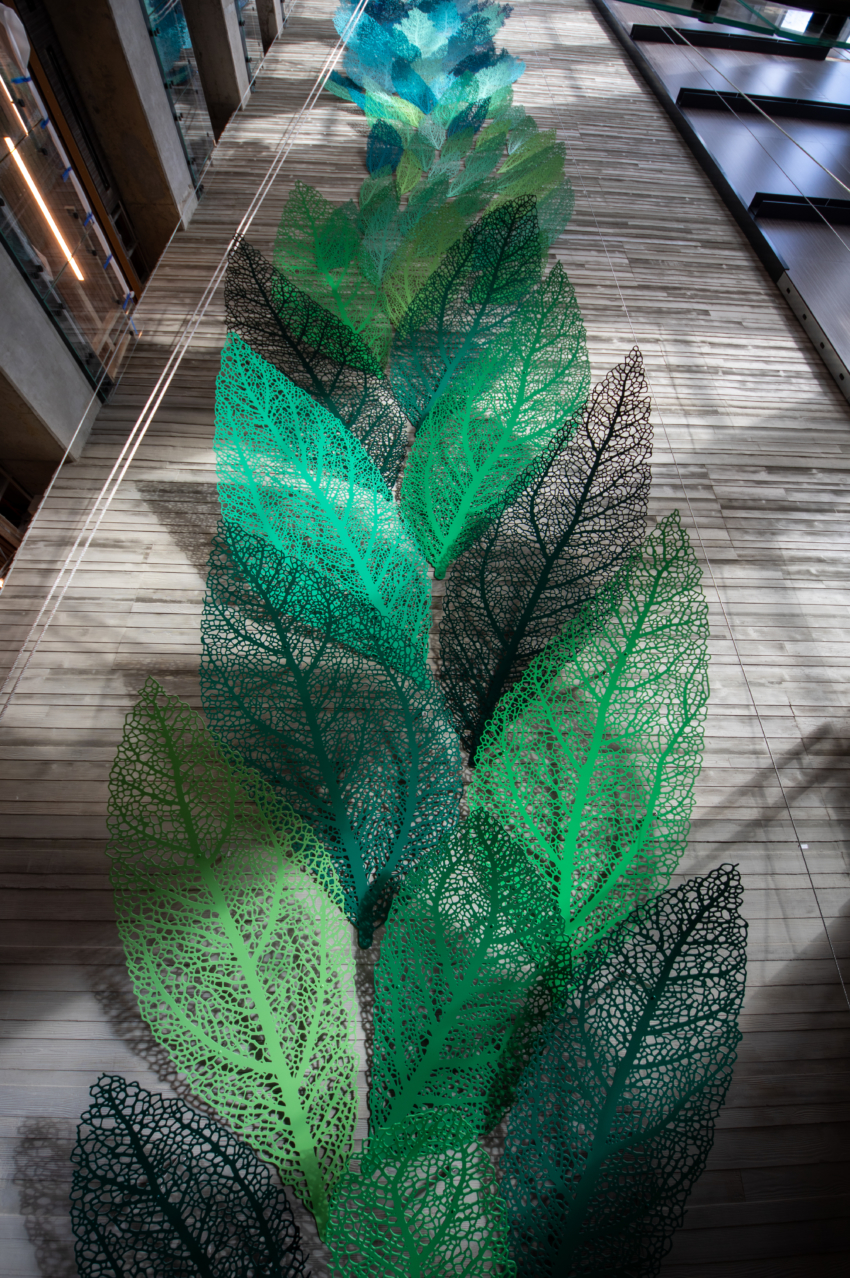
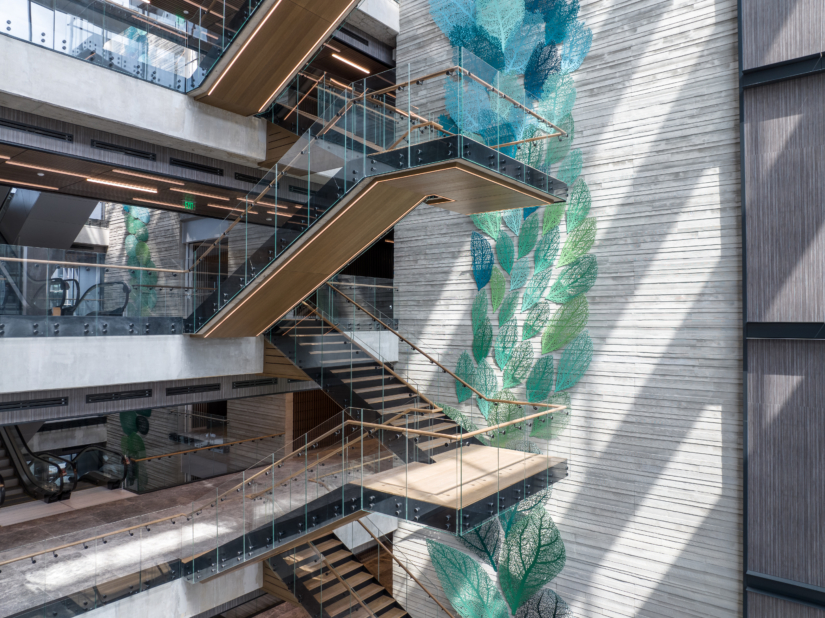
We recently created our first large scale public artwork. Soaring to a height of 120′, Xylem Arbor is an aggregation of bent metal leaves that climb up the atrium walls of the TEN30 corporate campus in Charlotte, North Carolina. The shape and pattern of the metal leaves evolves as the sculpture ascends. Each leaf features an intricate perforated pattern which is algorithmically generated based on simulations of natural processes.
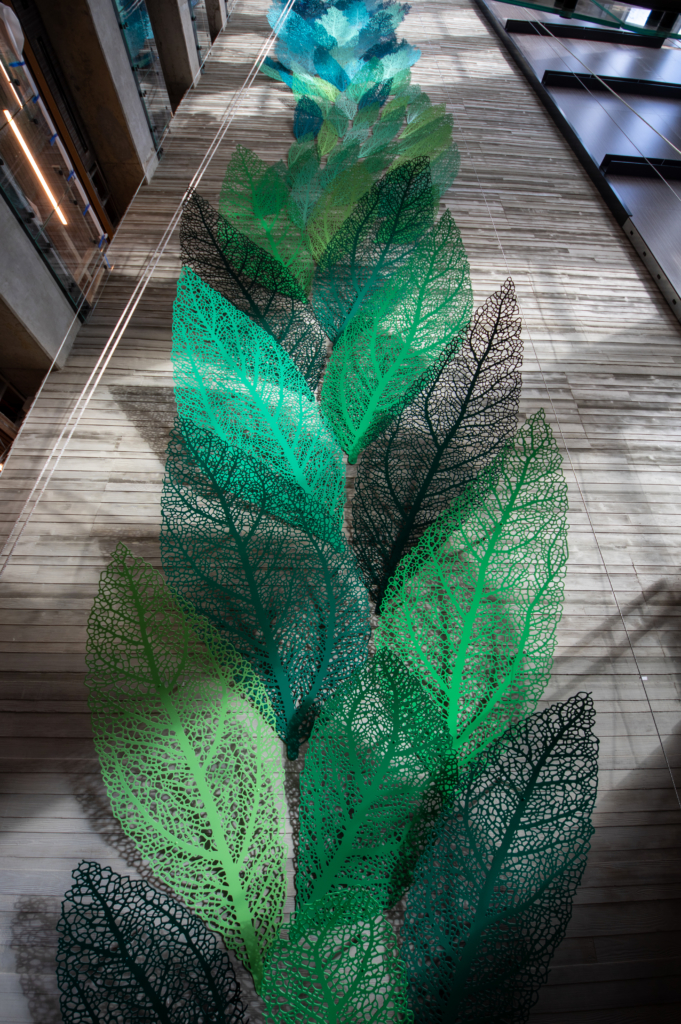
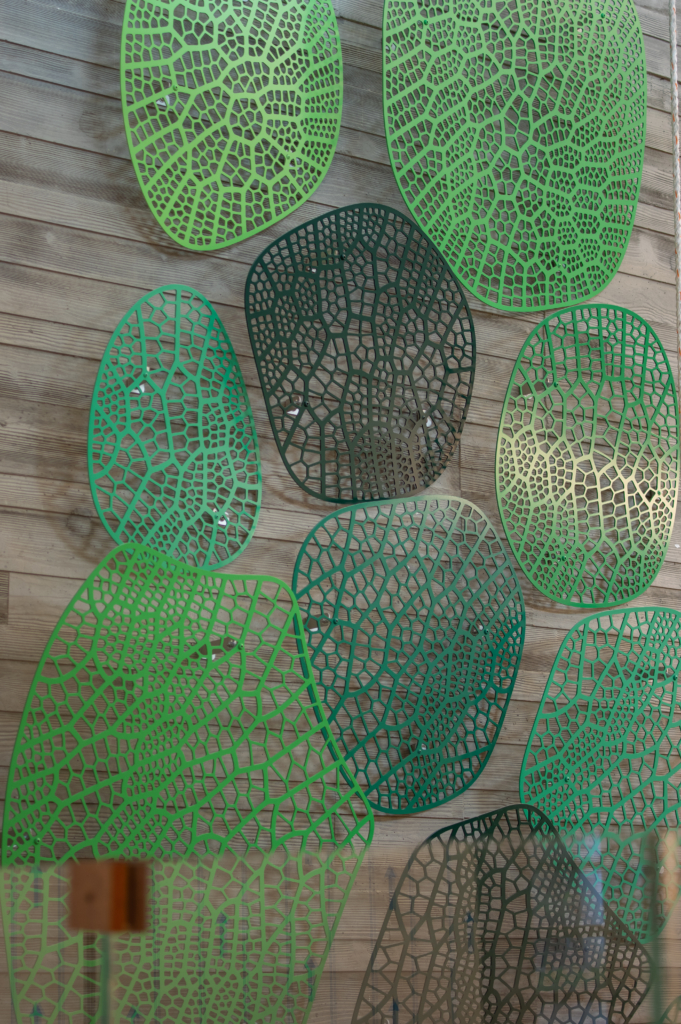
The Xylem Arbor explores patterns of circulatory systems in plants and throughout the biological world through the lens of science and computation. The sculpture is composed of 224 unique aluminum panels which span the 120’ atrium space. As you travel up the building, the patterns, shapes, and colors morph, evoking different structures from the natural world from lily pads to coral and leaf veins to dragonfly wings.
In nature, the closer you look, the more you can discover, and we want our designs to convey that same sense of wonder. This piece expresses our fascination with multi-scale structures, combining fabrication with geometric logic, and exploring new computational techniques.
At 120’ tall this is by far our largest work yet and it acts as the center piece of the building. This project used a complex generative design workflow to create the forms, arrangement, and intricate venation structures of the leaf elements drawing from research into leaf venation, coral growth, and cell structure. Generative design was also used to coordinate the fabrication, tracking and positioning of each unique element on site. Read on below to learn more about the design, software, fabrication and installation details.
There are two separate 120′ tall walls, one which runs along the staircase and other along an escalator. The east wall begins as monumental leaves towering at 12’ tall, and as you ascend what you thought were leaves become coral or dragonfly wings. The west wall investigates the microscopic to the macroscopic. It begins with stratified cellular patterns evoking the layers of a leaf, and gradually reveals vein structures becoming more leaf like at the top. There, the two walls meet with matching structures, displaying both veins and cells in leaflets that also speak to the cellular skylight of the atrium. The leaves on the east wall are bent into a curved shape and overlap.
Staircase installation – east wall
Escalator installation – west wall
Software
The project had two main software components. The first was a variation of our Corollaria system that we used to make the railing in our office. We modified it to design the overall layout and shape of leaves. We added morphing brushes to transform the cellular shapes into leaf-like ones. This layout also incorporated different zones of pattern to control how the leaves grow in each section.
The second piece of software grows the pattern inside each leaf with a combination of vein growth algorithms and anisotropic centroidal voronoi cells. This builds off of our previous Xylem and Hyphae projects as well as the body suit we designed for a Grimes music video. Each zone has different parameters leading to different types in each section. We input the layout from the previous step and grow each leaf sequentially. The patterns are grown in 2D and then bent into a 3D shape. We made sure that the flat shapes were bent realistically without any deformation so they would match how they would actually be produced. Each leaf has a constant bend radius (though it can vary between leaves), to keep the production as simple as possible. We output flat drawings that get used for production and 3D meshes that get used for rendering.
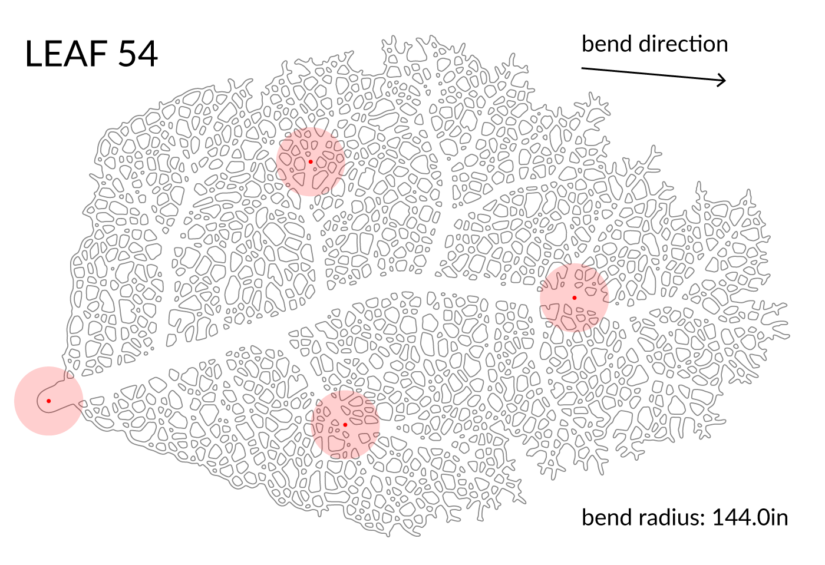
One technical detail is we switched to using the binary GLTF mesh format for this project. This is a relatively new standard that was created for 3D visualization on the web. This format matches how OpenGL stores mesh data, making it very fast to save and load. Since our geometry is very heavy, this dramatically sped up our rendering process. You can also encode materials in the format allowing us to directly import into Blender and render without having to do manual work.





Project development
In July of 2021, we were invited to participate in an RFQ for the new Centene East Cost Headquarters campus under construction in Charlotte, NC. We submitted artwork concepts for six different locations on the campus and were selected to pursue one of our concepts. We worked with the architects, LS3P, and our fabrication partner, James Coleman at Zahner from October 2021 through the summer of 2022 on the design development. We started from a simple rendering of a couple of algorithmically generated leaves to a complex installation of more than 220 unique bent aluminum leaves.
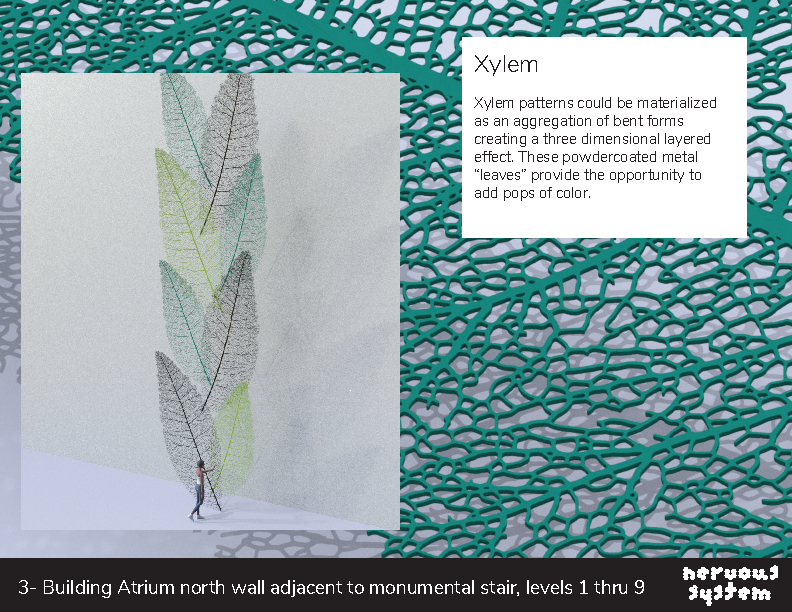
After the concept was selected, we spent a couple of months fleshing out a design system for the Xylem Arbor by creating software to help us arrange and grow the leaves. We started collaborating with James Coleman of SumPoint (formerly VP of Innovation at A Zahner Company) early in the process. Every leaf in the installation is unique and painted one of 16 colors. Each had to be installed in a precise location in a 120′ tall concrete atrium. Because of the complexity of fabricating, organizing and installing over 200 unique components we were grateful to get to work with James Coleman who has years of experience in figuring out how to engineer and fabricate innovative buildings and artworks.
Connectors
Due to the site constraints, we wanted to make the installation as simple as possible. Each leaf is mounted independently with 2 to 4 anchors. James designed the connection detail and coordinated the engineering to identify load constraints. Based on his feedback, we designed a system to automatically site anchor points on each leaf. Depending on the mass of the leaf, it was assigned 2, 3, or 4 anchors, though most leaves ended up with 3. One anchor was always at the base, while the others were sited at the largest solid point on the panel within specific regions. For 3 points those regions were 6 inches from the edge of the panel and between 1/2 and 2/3 up from the bottom, with one on the left and one on the right. This system allowed us to regenerate the entire design automatically while generating fabrication drawings, an anchor point layout and connector lengths all in about 30 minutes. This way we could tweak all aspects of the design from the overall layout to the character of individual patterns right up to the point that fabrication began. We also generated 3D surfaces of the design for rendering and detecting collisions between neighboring leaves.
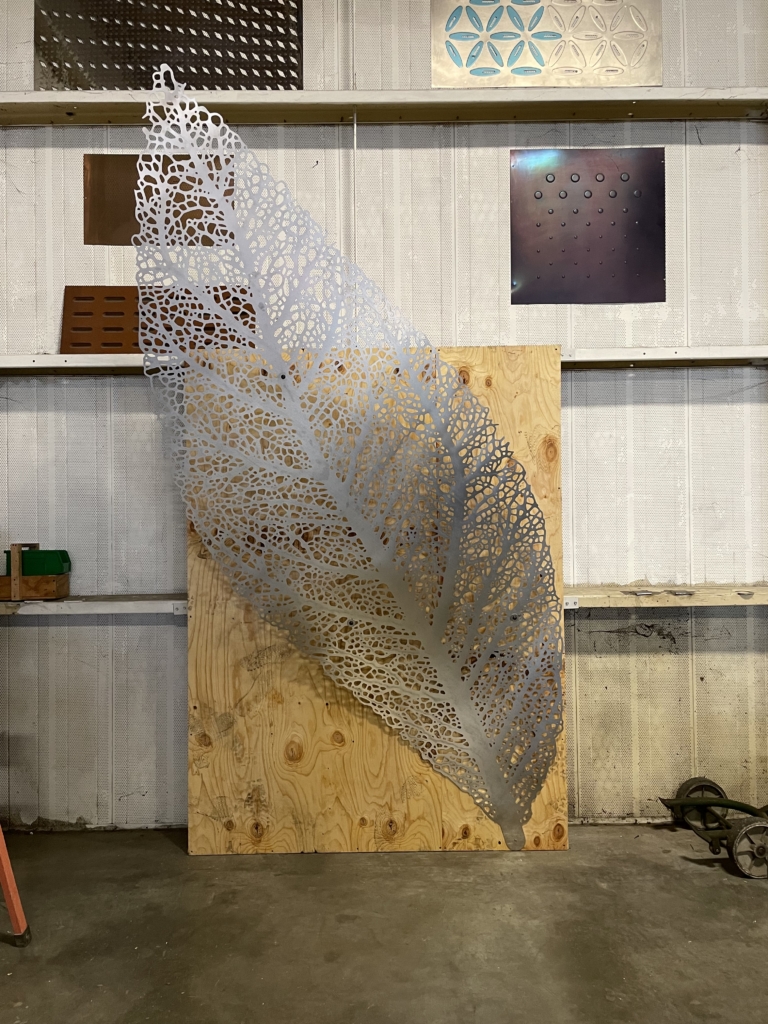
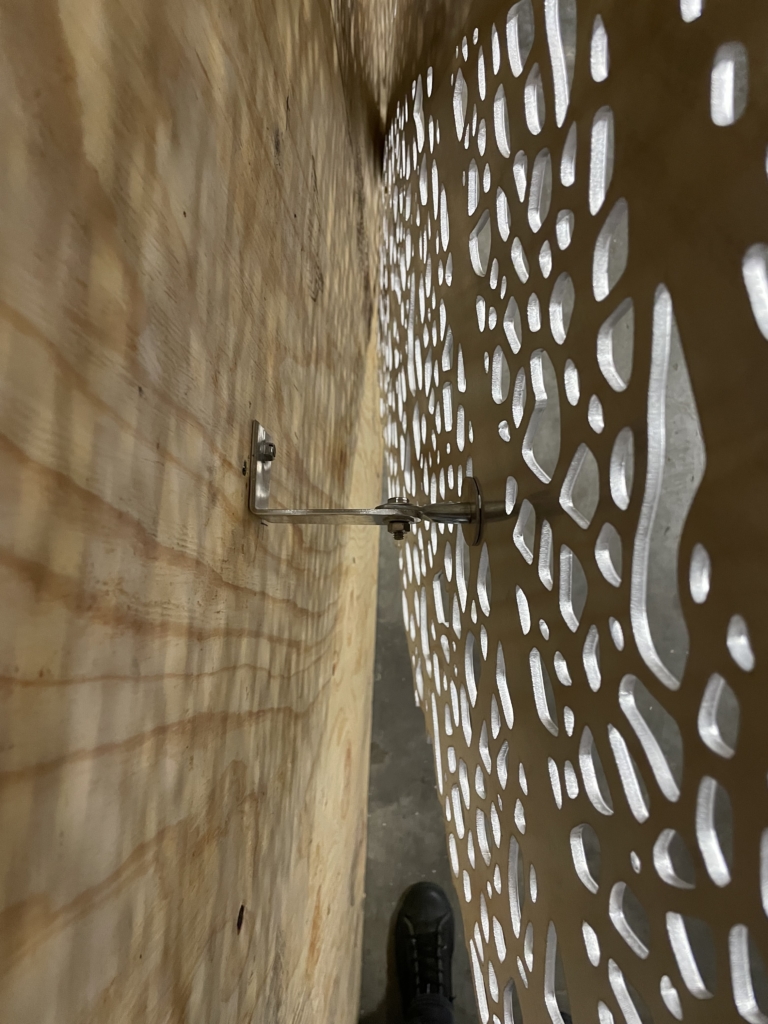
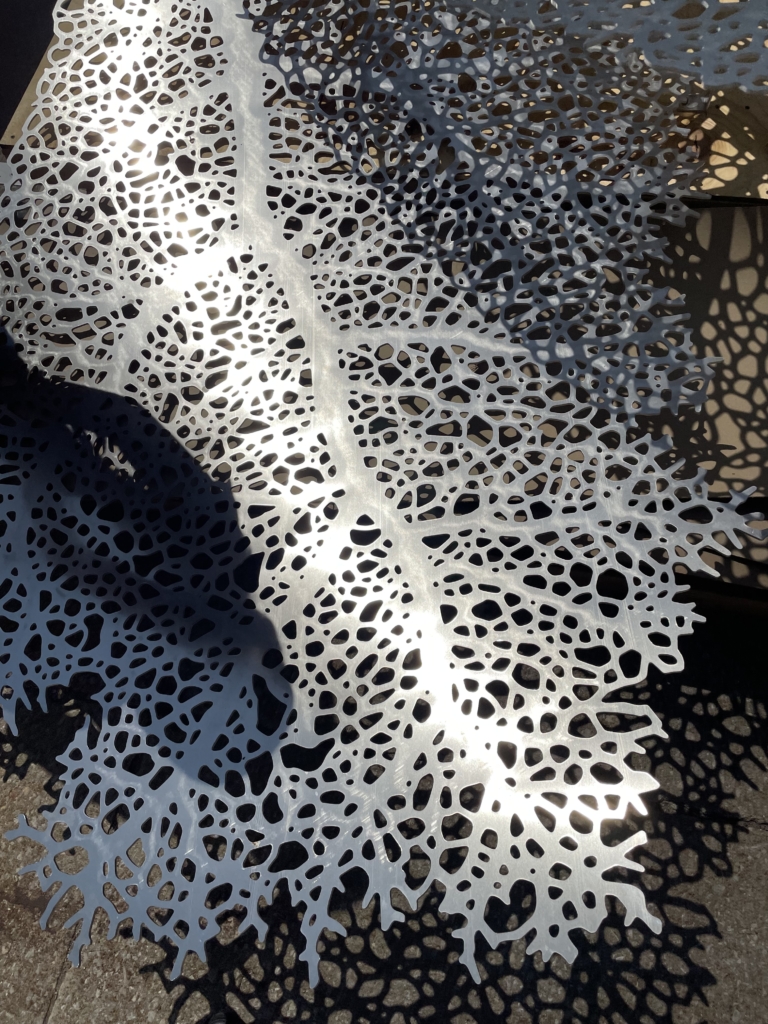
During August 2022 while we designed here in the Catskills, James worked at Zahner to create several full scale prototypes of our bent leaves in aluminum. He designed the connection details that allow each curved leaf to securely attach to the wall. At the same time, we produced a set of sample panels so we could see the scale of details, colors, and different paint finishes in real life.
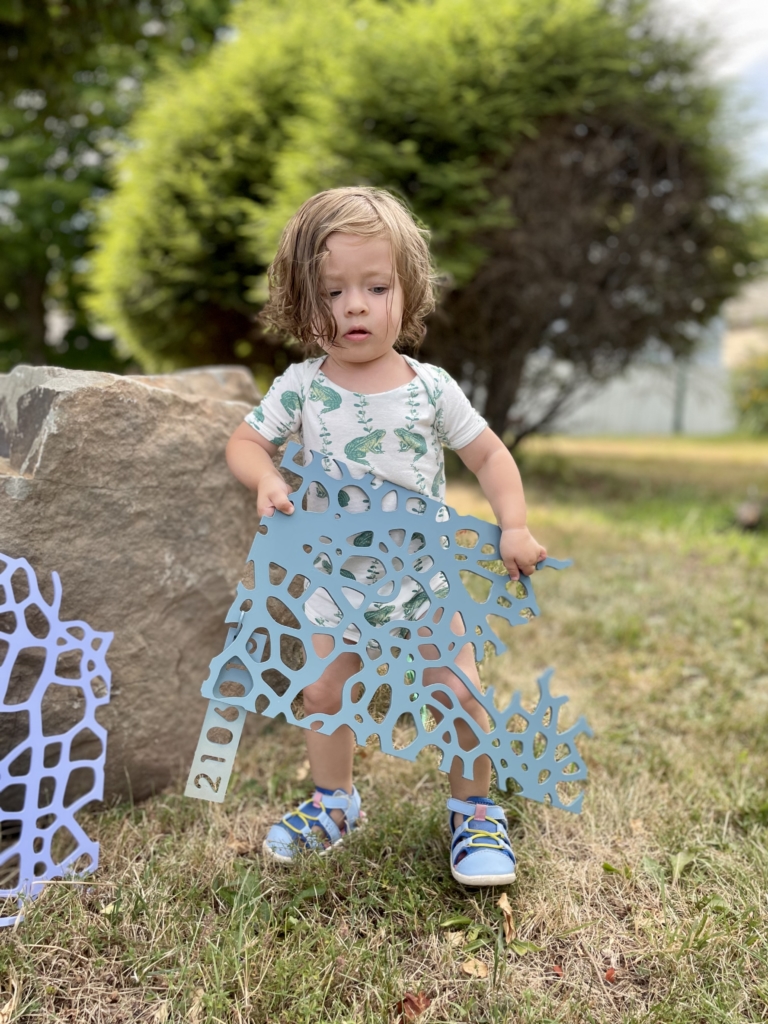

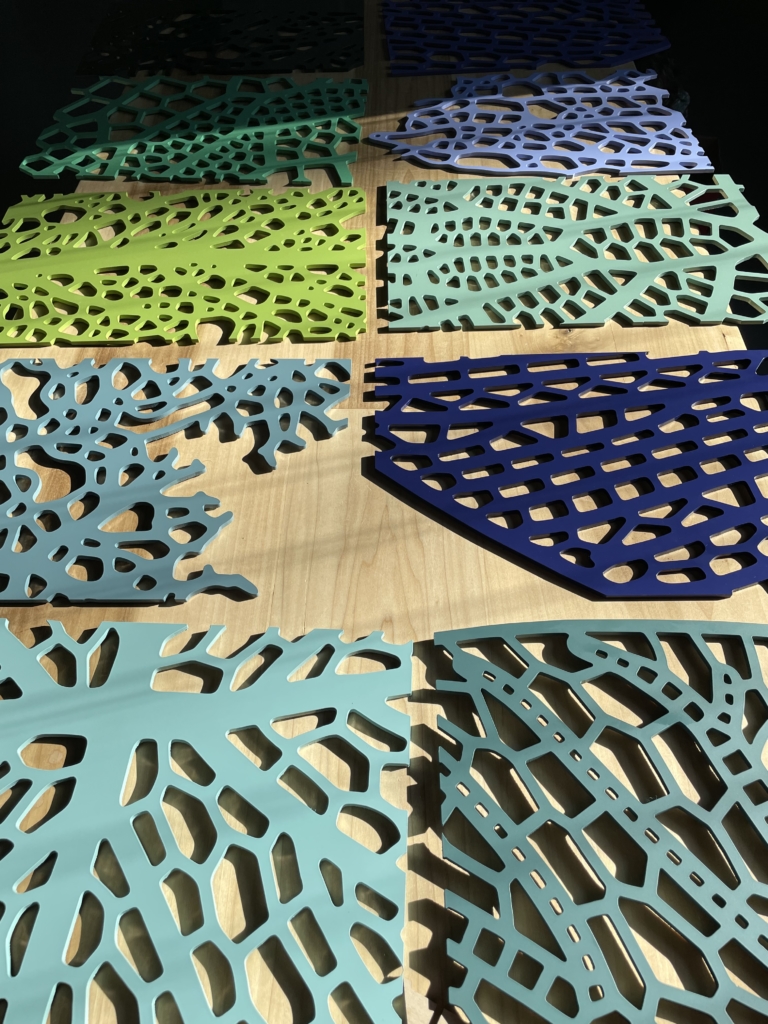
Fabrication
Fabrication began in earnest in September of 2022 and continued through November. The leaves were lasercut at Zahner’s facility in Texas. After cutting the parts were deburred and then rolled make them curved. A lasercut tag identifying each panel accompanied it through each step from lasercutting, bending, painting to install.






After rolling the leaves were painted one of 16 colors. Leaves were grouped by color rather than number or location in the installation to make painting easier. Bolts were also painted in each color so they could be color matched during the install.



Install
Installation started in early November while the leaves were still being fabricated. James travelled down to Charlotte to precisely map out attachment points for all the leaves while the installers got started at the top of the wall. Due to the narrow space, the installers had to work on a swing stage (essentially what window washers use to move along a building) instead of a lift.







Credits
Design: Nervous System (Jesse Louis-Rosenberg and Jessica Rosenkrantz, pictured above on left)
Client: Centene Corporation
Location: Charlotte, NC
Architect: LS3P
Fabrication and Installation: A. Zahner Company
A. Zahner Company team
Team Lead: James Coleman (now of SumPoint, formerly VP of Innovation at Zahner, pictured above on right)
Engineer: Burcin Nalinci
Shop Foreman: Brad Snelling
Installers: Tommy Humphrey, Aaron “Woody” Woodruff