Porifera – 3D printed ceramic jewelry
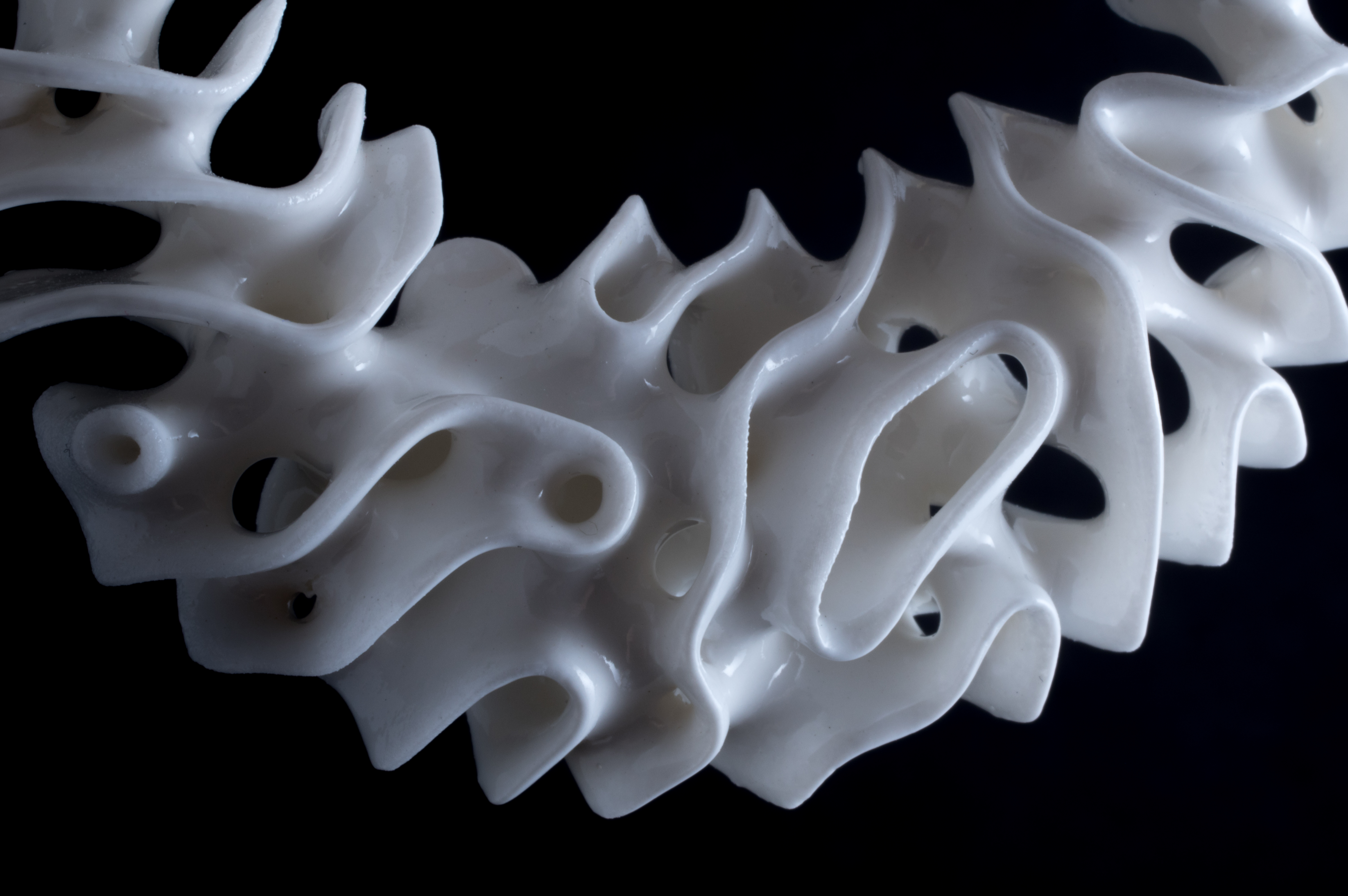
Porifera is a new jewelry collection by Nervous System inspired by the forms of deep-sea glass sponges and made in a new 3D-printed ceramic material. It is the result of two years of material experiments and research in collaboration with Formlabs. By combining new technologies and traditional crafts, ceramic 3D-printing lets us create intricate forms which cannot be manufactured by other methods. Each piece is finished by hand: sanded, glazed, and fired twice in a kiln up to 2340F, creating vitreous ceramic jewelry with a sumptuous glazed finish.
The sinuous, space-filling surfaces of the jewelry were inspired by the forms of glass sponges. Glass sponges build reefs with complex, porous architectures that are home to many species. Nervous System created custom software to computationally generate the designs. The software generates minimal surface networks along cellular scaffolds that adapt to different volumes and densities. The technique results in thin-walled 3D foams that can only be manufactured with 3D printing.
While Nervous System has been releasing 3D-printed jewelry collections since 2009, this is the first time we have manufactured a collection in house. The collection is now for sale online and will be available at the Nervous System pop up shop with Design Milk at ICFF in NYC from May 20-23. Formlabs is also launching the ceramic material today and has published an extensive user story about us.
Below we discuss the jewelry, inspiration, computational methods, and fabrication challenges behind this project in detail. This blog post is long so I’ll provide you with a table of contents:
- Porifera jewelry collection
- 3D printed ceramic with Formlabs
- Inspiration: glass sponges
- Generation: minimal surface foams
- 3D Printing Ceramic: challenges and techniques
- Thanks + Bibliography
Porifera Jewelry collection
Porifera jewelry is available in two materials: glossy white 3D-printed ceramic and golden brass cast from 3D-printed wax. The collection includes necklaces, earrings, and bracelets ranging in cost from $40 for a small pendant to $315 for a statement cuff. You can shop the full collection here. Below we show a few of our favorites.
3D-printed ceramic with Formlabs
There is something magical about ceramics. Humble materials like clay and sand are transmuted by heat into something vitreous and translucent. We have been working off and on with ceramics for several years using both traditional and digital methods; but we had not yet encountered a ceramic production process suited to our intricate, organic designs, one capable of meeting the constraints of making an affordable and durable product. With Formlabs’ new ceramic resin, we have finally been able to make that dream come true. We are now producing our first jewelry collection in ceramic, and it is manufactured completely in-house at Nervous System.
There are lots of ways people have been 3D-printing ceramics in the past few years. There are clay extruders, which many people are doing amazing with work (Emerging Objects, Unfold,Taekyeom) but the results are limited to larger forms and are low detail. There is powder-based printing, but the results are very porous and fragile, which makes it difficult to make fine structures. You can also 3D-print molds and cast into them, which is what Shapeways does, but making one-off molds is expensive and also limits the possible geometry.
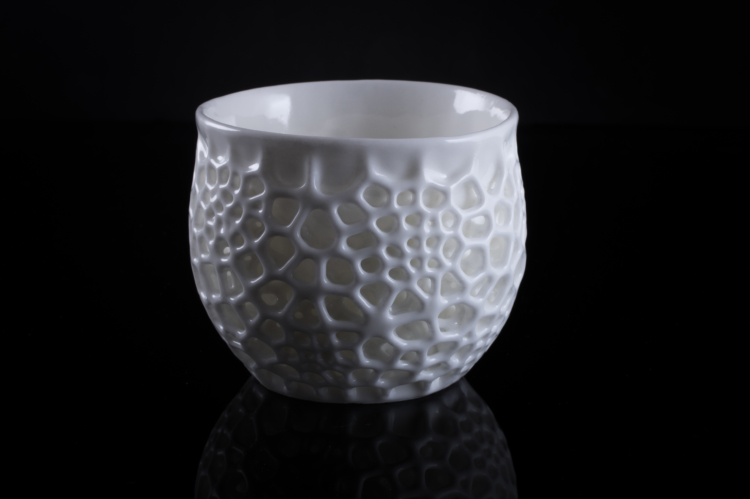
Two years ago we learned about SLA ceramic when we backed the Porcelite kickstarter by Tethon3d. SLA ceramic printing can produce objects with intricate details and has the robustness to make forms in ceramic we would not be able to make any other way. Since prototyping our Cellular Cup using Porcelite resin, we have been collaborating with Formlabs for the past couple years to develop and beta test their new 3D-printable ceramic material.
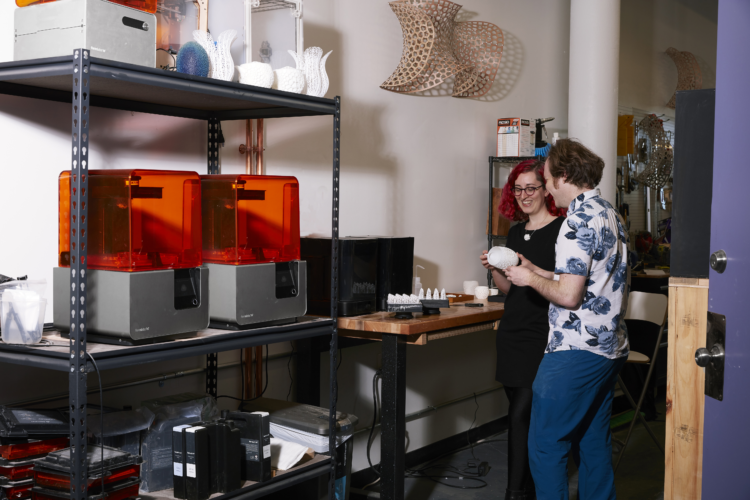
Inspiration: Glass Sponges
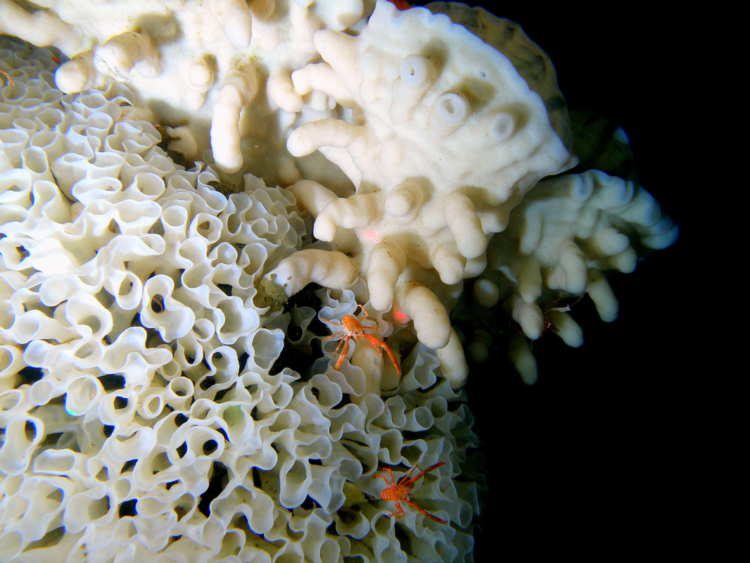
Sponges are among the weirdest and most ancient animals on earth and glass sponges are probably the weirdest and most ancient of all sponges. We’ve been fascinated by Sponges (phylum Porifera) since we started scuba diving 5 years ago. While diving, we have observed dozens of sponge species. They stand out because of their intense coloration, textured surfaces, and overall strangeness. While they are technically animals, they lack many of the fundamental features that distinguish animals from other lifeforms. Their bodies are asymmetrical and amorphous. Their cells, while organized, are not structured into tissues. They have no organs, nor respiratory, digestive, or nervous systems.
Glass sponges are even weirder because their body (which can grow to sizes of up to 1 meter across) is composed almost entirely of one giant cell with many nuclei. Within this giant cell they manufacture glass spicules which fuse together into a continuous lattice. Over time these glass skeletons build up to form reefs which are home to many species. The complex, porous architecture of these glass sponge gardens inspired the forms of this jewelry collection. Particularly, we were inspired by the species Farrea occa, which has recently been found to form huge reefs off the coast of Vancouver. Glass sponge reefs were common during the Jurassic period (about 200 million years ago) but were believed to be extinct until the 1990s when they were discovered by remote submersible vehicle off the western coast of Canada.
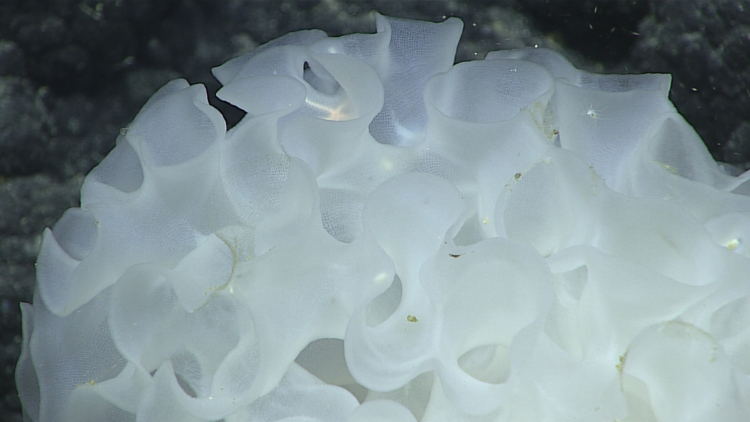
Generation: minimal surface foams
The structures of Porifera are the result of our ongoing research into developing 3D-printable, performative microstructures like foams. In the past few years, there has been much research into periodic minimal surfaces as efficient, lightweight structures. (Graphene gyroid, microscopic Schwarz D shell). The popular Gyroid as well as the Schwarz-D surfaces are space-filling shapes that are rigid while using a minimal amount of material. You can think of them kind of like a foam but as a continuous surface. These types of structures are especially beneficial for 3D printing because they form continuous, self supporting surfaces. Unlike typical lattice structures, they don’t have small cross-sections, which can often be a failure point in 3D-printing.
Alan Schoen, who discovered the Gyroid surface, explored much of the connection between periodic minimal surfaces and lattices. Inspired by this research, we developed a technique for generating space-filling minimal surfaces based on irregular lattices. Our technique allows us to conform the surfaces to specific boundaries and vary the density of points on the lattice, thereby shaping the designs.
Periodic minimal surfaces can be thought of as a parting surface between two skeletal graphs drawn on a lattice. For instance, the Gyroid has a skeleton of dual Laves graphs. If you take the Voronoi diagram of the lattice and remove the faces that intersect the skeletons, you get the topology of the minimal surface. Instead of a periodic lattice, we want to work with structure that can change through space.
The first step is generating a lattice. We want an efficient, ordered structure, like the diamond lattice that underlies the Schwarz-D surface, but with more flexibility. To generate structures with variable properties we use a technique for producing centroidally optimized Voronoi diagrams based on a paper called “Lp Centroidal Voronoi Tessellation and its applications” by Bruno Levy (link). We fill a given volume with points, then optimize their positions to fill space efficiently according to a density function we design.
The next step is to extract a skeleton from the lattice we generated. A minimal surface essentially divides space into two separate chambers, so to create our skeleton we partition the points of our lattice into two separate sets. The skeleton is the set of edges connecting points in the same set. We want to optimize our partition of points to maximize the area of the resulting surface. We can look at each point and ask: “if we switch the set of this point, will there be more surface in the surrounding cell or less?” We then go through an iterative procedure to maximize the total area.
Finally, we need to extract the resulting surface where the two chambers touch. We compute the Voronoi diagram of our lattice. Each face in the Voronoi diagram is associated with an edge in the dual Delaunay triangulation. If the edge connects two points in the same set, we delete the associated face. Then we evolve the surface using mean curvature flow to create a minimal surface, going from a faceted surface to a smooth one
3D-Printing Ceramic: challenges and techniques
Thousand year old traditional ceramics practices involve delicate processes that can be difficult to get right. (Chemical composition, moisture, temperature all play a part in the result). Adding 3D-printing into the mix only further complicates things. It’s definitely not a plug-and-play process, but the results are worth it.
Here are the basic steps: print parts, remove from supports, fire once, clean up parts, glaze, and fire again. We spent a lot of time at Nervous System developing techniques to get consistent parts with a perfect finish, including creating our own house-made glaze and custom firing schedules. Below we reveal all the tricks it takes to make this material work.
Printing
Stereolithography (SLA) 3D printers work by curing liquid resin with a UV light. A laser traces cross-sections of your design, solidifying the liquid layer by layer into solid plastic. Ceramic stereolithography works off the same principle, but the plastic resin has ceramic material in suspension. As the plastic becomes solidified, the ceramic particles are trapped there with them. Most ceramics processes have ceramic material in suspension with water, and the water is burned out in the kiln resulting in a dense part. With ceramic SLA, the ceramic is in suspension with resin which gets burned out to produce pure, solid ceramic.
Printing the ceramic resin can be tricky. It is much more brittle and heavier than other resins. Supports need to be thicker and more numerous. We place supports individually for each piece to ensure it prints consistently while limiting the amount of cleanup that needs to be done afterwards. The resin will also separate over time with the ceramic settling in the resin, so you need to make sure the resin in the tank and the cartridge is thoroughly mixed. The resin also won’t stick well to a raw build plate. You have to rough up the plate a bit with some sandpaper for it to stick. However, this is a delicate balance because too rough, and it will become almost impossible to remove. As we are printing, we constantly monitor the surface quality of our build plates, frequently re-sanding the surface with either 400 or 320 grit paper depending on what’s being printed.
Glazing
Our glazing process actually looks a lot like traditional ceramics, but it took us a while to get there. With all other 3D-printed ceramics we’ve worked with, we always fully fired the pieces and then glazed them with a low fire glaze. This worked well because the pieces weren’t actually as dense as normal ceramic. Their porosity meant glaze adhered well and evenly to the surface. Formlabs ceramic fires to an almost glass-like density, which is great, but it means that glaze does not stick well. When we tried to dip them fully fired, we got funky results.
Instead, we do something like a traditional bisque firing. In the first firing, which is actually a burnout of the plastic resin, we fire to a lower temperature, cone 05 or ~1900F. We weren’t sure if this would work, since this isn’t a normal ceramic. Would the pieces be strong enough to handle if we burned off the resin but didn’t fully sinter (melt) the parts together? Luckily, the results were perfect, still fragile like any bisqueware would be, but definitely workable. This leaves porous parts that gladly accept glaze. One note is that you need a special setup during the burnout to vent the fumes. Kilns often have some ventilation, but it not very strong and more about airflow within the kiln than removing noxious vapors. We do our burnouts in our spraybooth room with a very strong fan.
In the bisque state, we clean up the areas where supports were attached. The bisqueware is extremely easy to sand. The pieces are then dipped in our in-house cone 10 glaze. The glaze firing is then a completely conventional firing to just shy of cone 10 (2320F). Note, we fire to cone 10 because that is where this ceramic fully sinters to have the most strength, but it’s hotter than most ceramics are fired these days.
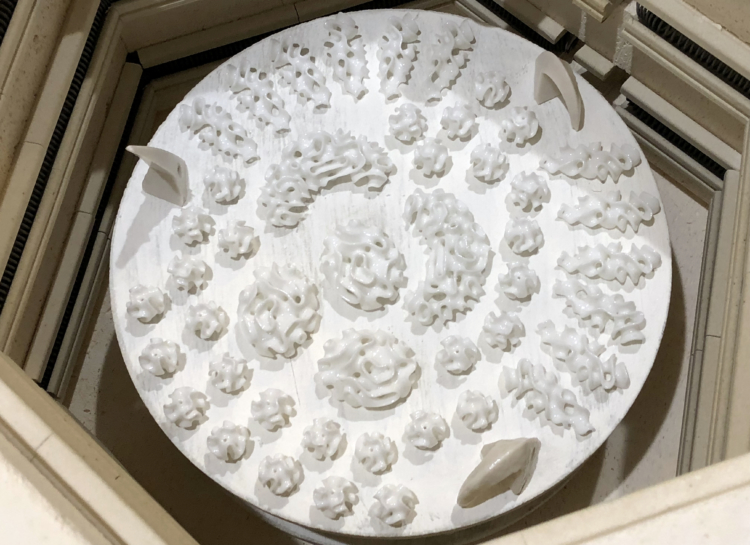
Geometry is very important with ceramics. As with anything you print on a desktop printer, you want it to be self supporting to limit the amount of support you have to print. However, self-supporting geometry is even more important with ceramics since when you fire it, it becomes almost liquid and will slump and crack if unsupported.
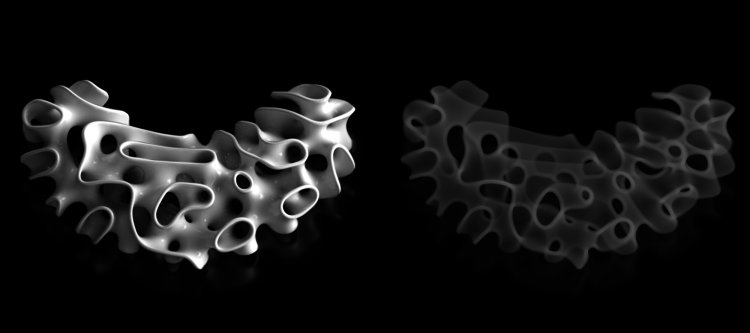
Acknowledgements
Formlabs, especially Amos and Gaetan
Sally Leys, University of Alberta – sponge research and photography
Elena Kulikova – photography
Christina Wen – model
Megan Sutherland and Maddison Kate – makeup
Nadya Peek – proofreading
Construction – music
Bruno Lévy and Yang Liu. 2010. Lp Centroidal Voronoi Tessellation and its applications. In ACM SIGGRAPH 2010 papers (SIGGRAPH ’10), Hugues Hoppe (Ed.). ACM, New York, NY, USA
Seung Chul Han, Jeong Myung Choi, Gang Liu & Kiju Kang. 2017. A Microscopic Shell Structure with Schwarz’s D-Surface. Scientific Reports, volume 7
Alan Schoen. Triply-periodic minimal surfaces.
Glass Sponge Reefs – the basics.
eyeonjewels
These designs are very unique and beautiful. Thanks for sharing.
Let’s Paint the Town Green: Mathematical Surfaces Behind Butterflies’ Colours - AMSI Vacation Research Scholarships 2018/19
[…] and a good dose of computer visualisation, and some inspiration from arts and nature. ‘Nervous system’, a Boston-based arty 3D printing start-up company, describes an algorithm for modelling […]