Data-customized midsoles with New Balance
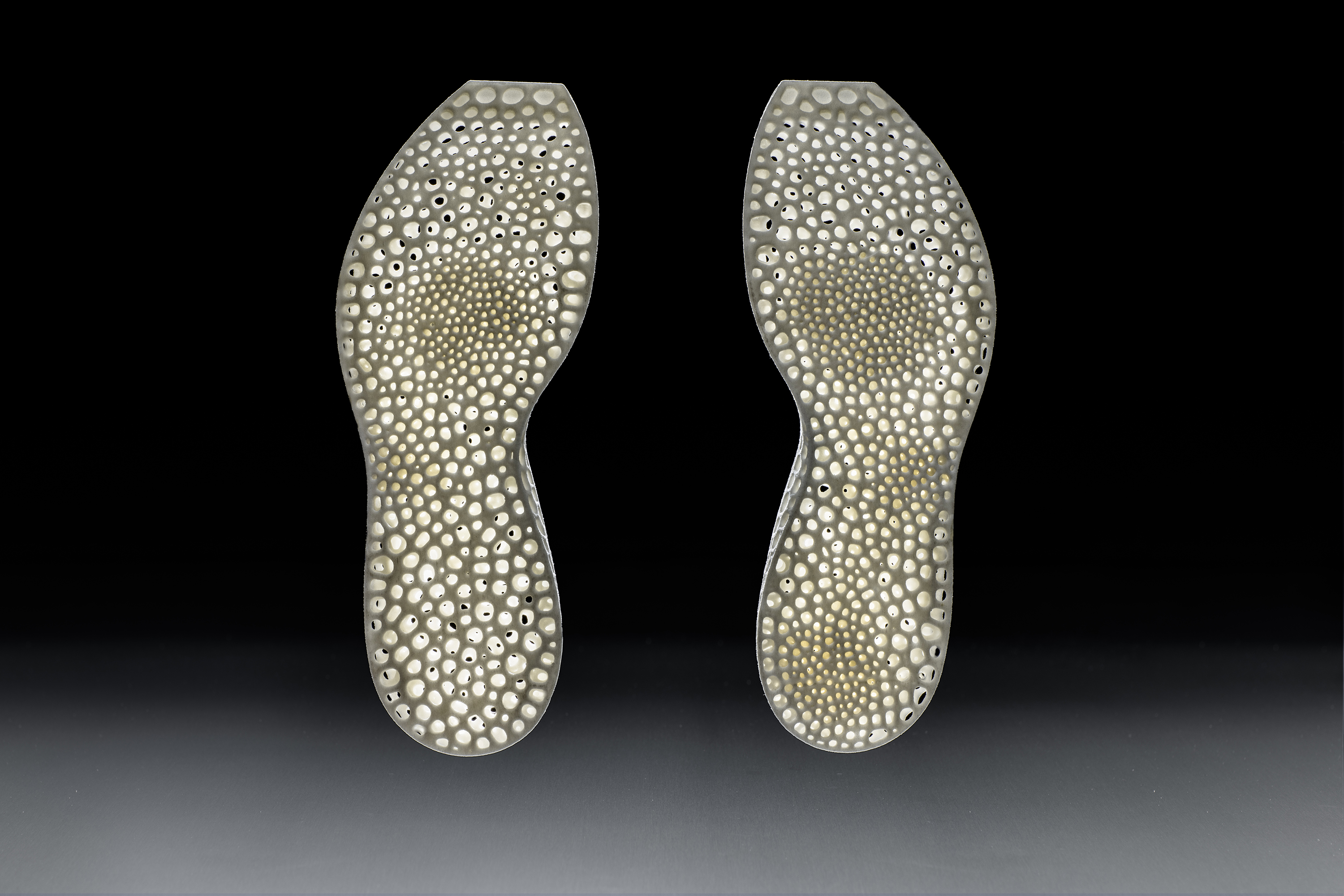
Nervous System is working with New Balance to develop functional 3D-printed midsoles for performance running shoes. We have created proprietary systems to generate midsole designs from pressure data from runners, making it possible to create variable density cushioning that is customized to how a person runs. This ongoing project has given us a unique opportunity to apply our generative design techniques to a new domain.
New Balance will start selling shoes with 3D-printed midsoles in April 2016, with a customized version to debut in 2017. You can read more about that in their press release.
Unlike traditional midsoles, these are not a uniform foam but a structure that can be adapted to different runners.
The midsole on the left is generated from the underfoot pressure data of a person who runs with a midfoot strike and the right midsole is generated from heel strike data.
These midsoles are printed using Selective Laser Sintering in a new flexible elastomer.
Design Approach
New Balance came to us with a problem. They wanted to improve the design and creation of their 3D-printed midsoles to better adapt to performance data from a runner. They have been working on 3D-printing components for athletic shoes for several years and in 2013 released shoes with 3D-printed spike plates. However, working with a complex, high performance 3D structure creates challenges that we could help with.
data to design
For the midsole, the primary data we are working with is pressure data from a runner’s foot strike. New Balance has worked extensively on data to design processes for previous projects like Fresh Foam. We had multiple sets of data available to us that were captured at the New Balance Sports Research Lab in Lawrence, MA. The data is recorded by a grid of sensors underfoot that show the force as the foot hits ground and pushes off through time.
Our first question was, is this a optimization problem? There has been a lot of work lately looking at structural optimization in design such as Autodesk’s Dreamcatcher. However, we quickly decided that wasn’t quite the right approach for this project. First, the scenario is quite complex. We aren’t looking at a static load bearing structure, but one that has highly variable forces where the desired response might change over time. Does the pressure on landing have the same significance as the push off pressure? Additionally, there’s still a lot about the physiology of running that we don’t understand. What function do we actually want the midsole to have? If we can’t come up with a precise numerical definition for that, we can’t optimize for it.
Instead, we decided to create a platform that would allow us to experiment with variable midsoles that could respond to data in different ways. Rather than optimizing, we want to be able to quickly test different ideas and get them on runners’ feet, see how they feel and perform, and iterate. Our first approach is to think about the midsole as a foam, but instead of a traditional, uniform microscopic foam, we create a highly controllable anisotropic, macroscopic foam structure.
Foam structures are three-dimensional arrays of cells. They have a low relative density and are highly porous giving them the unique property of being both lightweight and strong. While man-made foams are rather uniform, the foams we see in nature like wood and bone are highly variable in scale and direction, enabling specific material properties in different zones. We wanted to use the running data to design foams that geometrically adapt to different forces.
Other Concepts
We also explored other ways of interpreting the data in a midsole. One series of experiments explored generating directional structures for the midsole that follow the gradient of the pressure data. We wanted to look at how the midsole could more explicitly mirror the data used to generate it. The lines accentuate how the pressure data reflects the anatomy of the foot, revealing maxima in the heel, forefoot, and toes.
Another set of prototypes looked at generating more loosely interconnected structures based on our Hyphae system which grows networks inspired by how veins form in leaves.
Susan Emmerson
I am very interested in getting these shoes when they are available. Keep me informed!
3D printing and the future of manufacturing | Future Lab - Studying security trends
[…] Nervous System and New Balance collaborated to develop 3D printed midsoles for running shoes with the objective of customizing to the needs of athletes and customers. Read more. […]
Nervous System collaborates with New Balance on 990S shoes | Nervous System blog
[…] New Balance’s innovation team since 2015 on various projects including the Zante Generate shoe, data-customized midsoles, and design customization software. The new 990 Sport sneakers feature a 3D-printed heel component […]